Feinbohren, Schruppen, Aufbohren großer Durchmesser – unabhängig von der Anwendung ist es wichtig, dafür das richtige Werkzeug zu finden. Die Bearbeitung von Bohrungen, ob bei der Lohnfertigung kleiner Serien oder in der industriellen Produktion mit großen Stückzahlen, erfordert Präzision. Wenn ein
Ausdrehwerkzeug auf einen bestimmten Durchmesser eingestellt wird, wirkt sich dies auf die Auswuchtung des Werkzeugs aus, was sich wiederum auf die Rundheit der Bohrung, die Oberflächengüte und auch die Vorschubgeschwindigkeit des Ausdrehwerkzeugs auswirkt. Während bei Aufträgen mit geringen Volumina in der Regel vielseitig einsetzbare Aufbohrwerkzeuge vorteilhafter sind, kommen bei Aufträgen mit hohem Volumen und bei Aufträgen mit engen Toleranzen oder hohen Anforderungen an die Oberflächengüte für jede Anwendung spezielle Werkzeuge zum Einsatz.
Ein wichtiger Tipp ist, das Werkzeug so kurz wie möglich zu halten, um die Durchbiegung zu verringern, die zu einer schlechten Oberflächengüte führen kann. Das Verhältnis zwischen Länge und Durchmesser ist bei Ausdrehwerkzeugen extrem wichtig. Im Idealfall beträgt das Länge-Durchmesser-Verhältnis bei ungedämpften Werkzeugen 5 x D oder weniger, während beim Einsatz von Schwermetall-, Hartmetall- und schwingungsgedämpften Modulen Bohrungen mit bis zu 10 x D möglich sind. Natalie Wise, Produktmanagerin für die Produktgruppe der Ausdrehwerkzeuge von Allied Machine, erklärt: „Unsere NOVITECH-Module nutzen eine viskoelastische Flüssigkeit, um Vibrationen zu minimieren und Bohrtiefen bis zu 10 x D zu ermöglichen. Diese schwingungsdämpfende Technologie erhöht nicht nur die Lebensdauer der Ausdrehwerkzeuge, sondern verlängert auch die Lebensdauer der Spindel, während sie eine hervorragende Oberflächenqualität erzeugt.“ Bei modularen Aufbohrsystemen ist es wichtig, die für eine Aufgabe ausgewählten Komponenten zu berücksichtigen und dann zu versuchen, alle unnötigen Längen zu entfernen. Denn es gilt: je kürzer und robuster, desto besser.
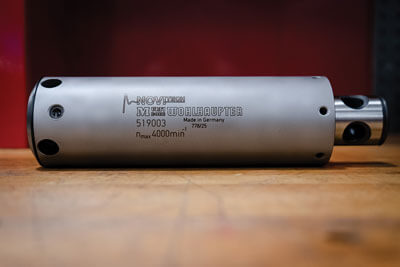
Bei Aufbohranwendungen mit großen Durchmessern ist es wichtig zu prüfen, ob die geplante Maschine über eine Pinole verfügt. Eine Pinole ist ein Stößelsystem, das die Spindel über ihre Standardposition hinaus verlängert. Die Pinole, auch Bohrspindel genannt, gibt es in verschiedenen Durchmessern, in der Regel zwischen 125 und 250 mm; sie kann einen Verfahrweg von mehreren Metern haben. Beim Ausspindeln von großen Durchmessern ermöglichen Pinolen, das Ausdrehwerkzeug zu verkürzen, was wesentlich zum Erfolg der Bohrung beiträgt.
Augenmerk gilt auch den mit den Bohrwerkzeugen verwendeten Wendeschneidplatten. Geeignete Geometrien und Sorten sollten auf der Grundlage des zu bearbeitenden Materials, der abzutragenden Aufmaßmenge und der erforderlichen Werkzeugstandzeit ausgewählt werden. Darüber hinaus wirken sich Beschichtungen und der Radius der Schneidplatten, der zur Schnitttiefe passen sollte, auf die Leistung des Werkzeugs aus. Auch die Spanbrecher beeinflussen die Leistung, da die Spankontrolle oft vom Spanbrecher der Wendeschneidplatte abhängt.
Nicht nur das Werkzeug, auch die Maschine selbst muss passen. Bei großen Durchmessern können beispielsweise das Gewicht des Ausdrehwerkzeugs und das Kippmoment Probleme bereiten. Beides wirkt sich auf die Funktionalität des Greifersystems aus, das das Werkzeug in der Spindel hält, und auf das Werkzeugwechselsystem, das entweder den Werkzeugwechsel durchführt oder das Werkzeug in seinem Magazin speichert. Ein weiteres Problem kann die verfügbare Leistung sein, die mit dem Durchmesser des Werkzeugs und der Menge des zu entfernenden Materials kämpft.
Die passende Aufbohr-Werkzeuglösung lässt sich am Ende insbesondere auf der Grundlage der Anforderungen der Anwendung auswählen. Modulare Verbindungen sind von großem Vorteil, denn sie verringern nicht nur den Bedarf an speziellen Verlängerungen, sondern ermöglichen auch eine einfache Anpassung an die Maschinen. Mit einer modularen Verbindung können die Schäfte schnell für verschiedene Spindeltypen ausgetauscht werden; außerdem bietet sie maximale Flexibilität eines Systems, das mehrere vielfältige Kombinationen ermöglicht. Bei der Verwendung einer modularen Verbindung kann ein Werkzeug so kurz und robust wie möglich gestaltet werden. Durch die Optimierung der modularen Komponenten, die einem Ausspindelwerkzeug seine Länge geben, wie Verlängerungen, Reduzierungen und verlängerte Grundaufnahmen, kann das L x D-Verhältnis erheblich reduziert werden. Bei einer 75 Millimeter langen und 300 Millimeter tiefen Bohrung kann ein Komplettwerkzeug beispielsweise ein Verhältnis von 7 x D ergeben, während ein anderer Zusammenbau mit derselben Länge nur ein Verhältnis von 5 x D aufweisen kann. Die 5 x D-Kombination wird letztlich besser abschneiden als die 7 x D-Lösung, insbesondere wenn man die Zykluszeit berücksichtigt.
Zusätzlich zu den modularen Verbindungen ist abzuwägen, ob ein einzelnes Ausdrehwerkzeug oder ein Ausdreh-Set die beste Option für eine bestimmte Anwendung ist. Während Kits hohe Flexibilität bieten, sichern einzelne Ausdrehwerkzeuge Konsistenz, wenn sie am meisten benötigt wird. Für Werkstätten ist es oft vorteilhaft, Ausdreh-Sets zu verwenden, um mehrere Durchmesserbereiche je nach den individuellen Anforderungen zu ermöglichen. Solche Kits eignen sich vor allem für Prototypen, Kleinserien, Einzelstücke mit geringer Stückzahl und Reparaturabteilungen. Ausdrehsätze sind also ideal für Zerspanungsmechaniker, die ein Ausdrehwerkzeug für eine Vielzahl unterschiedlicher Aufgaben suchen. Umgekehrt werden einzelne Ausdrehwerkzeuge häufiger in einer Hochproduktionsumgebung eingesetzt. Sie sorgen für niedrigere Werkzeugkosten und sichern die für einen engeren Durchmesserbereich erforderliche Reproduzierbarkeit.
Kundenspezifische Ausdrehwerkzeuge sind eine weitere Option, die bei der Auswahl von Werkzeugen in Betracht gezogen werden sollte. Von der Reduzierung der Zykluszeit und der Verbesserung der Qualität eines Bauteils bis hin zu Kosteneinsparungen durch die Kombination mehrerer Bohrungen in einem Arbeitsgang bieten Sonderwerkzeuge viele Vorteile. Während die meisten Ausdrehanwendungen mit Standardwerkzeugen ausgeführt werden können, gibt es immer wieder sehr spezielle Anwendungen, die entsprechende Lösungen erfordern. Komplexe Bohrungsprofile und Beschränkungen der Werkzeugmaschinenmagazine brauchen ein Werkzeug das mehrere Durchmesser gleichzeitig bearbeiten kann.
Eine weitere Herausforderung bei der Auswahl des Ausdrehwerkzeugs ist die geforderte Oberflächengüte. Ausdrehwerkzeuge können eine sehr feine Oberflächengüte erzielen, insbesondere bei Verwendung einer Wendeschneidplatte mit Wiper-Geometrie.
Auch das Kühlmittel kann dazu beitragen, die gewünschte Oberflächengüte zu erzielen und die Standzeit des Werkzeugs zu verbessern, solange das Kühlmittel aufrechterhalten wird. Dennoch muss das Kühlmittel unter verschiedenen Bedingungen sorgfältig ausgewählt werden:
- Integrierte digitale Werkzeuge: Einige digitale Bohrköpfe haben einen begrenzten Kühlmitteldruck. Wird dieser überschritten, kann dies zu Schäden an den internen Komponenten des Bohrkopfs führen. Viele Werkstätten verwenden Pumpen mit einem Druck von 70 bar, was zum Versagen von Dichtungen führen kann. Insbesondere beim Feinbohren ist dieser Kühlmitteldruck nicht erforderlich. Die Späne sind oft so klein, dass es für die Späneabfuhr zu viel ist. Bei korrekter Spanabfuhr sind 20 bar vollkommen ausreichend.
- Schwere Schruppanwendungen: Wenn die zu entfernende Materialmenge größer ist als die Differenz zwischen der Bohrungsgröße und dem Körperdurchmesser, kann die Spanabfuhr behindert werden, so dass das Kühlmittel in diesen Fällen eine große Rolle spielt
- CBN-Wendeschneidplatten: CBN verträgt Wärmeschocks nicht gut, was bei der Verwendung von Kühlmittel vorkommen kann. In den meisten Fällen wird CBN trocken gefahren, um Probleme zu vermeiden.
Letztlich eignen sich für interne Komponenten in Feindrehwerkzeugen am besten lösliche Kühlmittel, da Kunststoffe interne Schäden verursachen und die Genauigkeit verringern können.
Die Spanabfuhr ist zwar eher ein Problem beim Schruppen als beim Schlichten, aber die Wahl der Wendeschneidplatte kann hier einen entscheidenden Unterschied machen. Die Geometrien sollten sorgfältig auf der Grundlage des zu bearbeitenden Materials und der Menge des zu entfernenden Materials ausgewählt werden. Zu berücksichtigen ist auch der Durchmesser des Werkzeugkörpers und zusätzlicher modularer Komponenten wie Verlängerungen und Reduzierstücke im Verhältnis zur abzutragenden Materialmenge. Wenn das zu entfernende Material die Differenz zwischen der Bohrungsgröße und dem Körperdurchmesser überschreitet, kann die Spanabfuhr behindert werden; dies kann zu einer Beschädigung des Aufbohrwerkzeugs und möglicherweise des Werkstücks führen. Da gilt „Je kürzer der Span, desto besser ist die Spanabfuhr“, führt eine sorgfältige Auswahl des Werkzeugs und der Anwendung selbst zur besseren Spanbildung.
Auch künftig wird es Ausdrehwerkzeugen weitere Verbesserungen und Innovationen geben. Technologien, die bisher nur in Einzel- oder Kleinserienanwendungen zum Einsatz kommen, werden auf alltägliche Anwendungen übertragen und sind damit leichter zugänglich und kostengünstiger. Die meisten, wenn nicht alle verstellbaren Feinbohrwerkzeuge werden digital sein. Feinbohrköpfe lassen sich in Zukunft über ein separates Modul oder über das Internet einstellen. Die Zukunft der Bohrungsbearbeitung hat längst begonnen!